AXIS PITCH (AXP)
Founded in 2022 focused on Aerospace and Defense Manufacturing, Axis Pitch (AXP) has consistently delivered complex and advanced system components, some of which you've likely seen or used.
In June of 2023, during an all-hands meeting, we asked ourselves "what can we do better in the manufacturing space, with the team knowledge and abilities here?" Within a week we completed our first putter prototype, and in September of 2023 we revealed "The Front 9".
We're a small, agile team of experienced machinists, designers, programmers, helicopter pilots, champion professional fighters, and of equal importance - golfers. We're not set up with foreign supply lines to meet that seductively priced $500 putter that some people equate with the highest quality. AXP is focused on bringing you 100% American Made equipment, cut right here in the heart of Texas, and we believe it's more important to focus on quality of processes and bringing you a truly unique tool to your game.
Our objective is to constantly push the ball forward for this industry, with previously unseen approaches to design and machining, bringing you more than the tired designs of the last 50 years.
And we're just getting started.
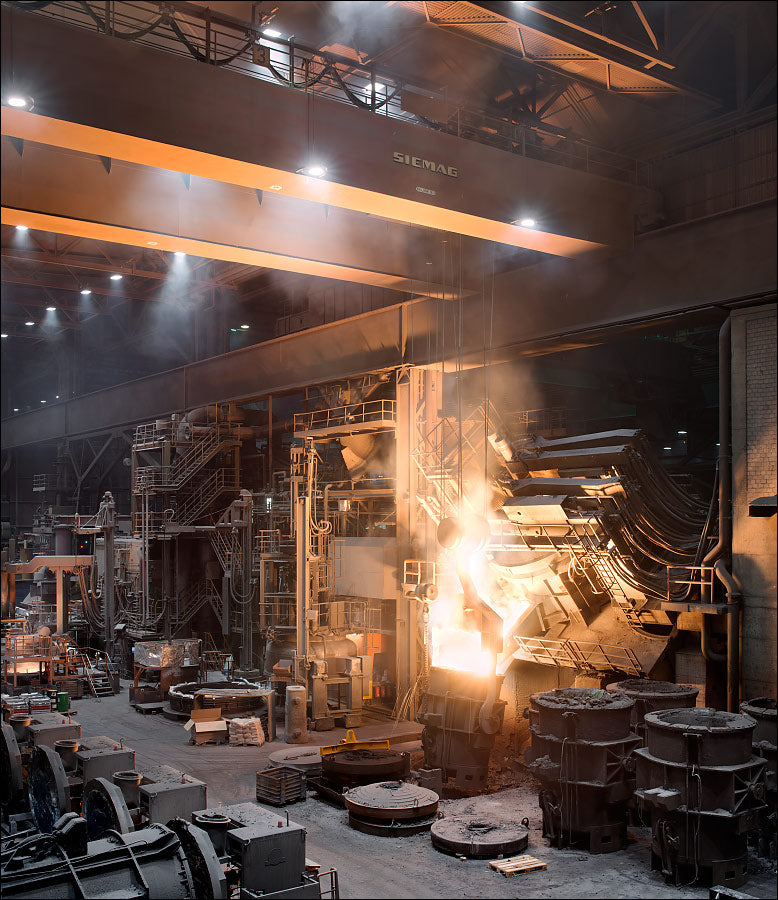
the foundation
MATERIAL
At AXP we use exclusively German 303 Stainless Steel, often referred to as GSS within the golfing industry. Each delivery we receive is accompanied by a MTR, Mill or Material Test Report, indicating the chemical analysis of the stock, along with the grade and mechanical properties from the German foundry. Each bar is inspected again by our staff, both for chemical composition, and defects before being accepted.
Some competitors claim to use German Stainless Steel, but may use second-hand Stainless from substandard sources. All AXP putters use 303 sourced directly from German foundries, using their unique formula.
We track and associate all putters with their respective MTRs, and we can provide the exact testing report for yours; the only way to know a material source.
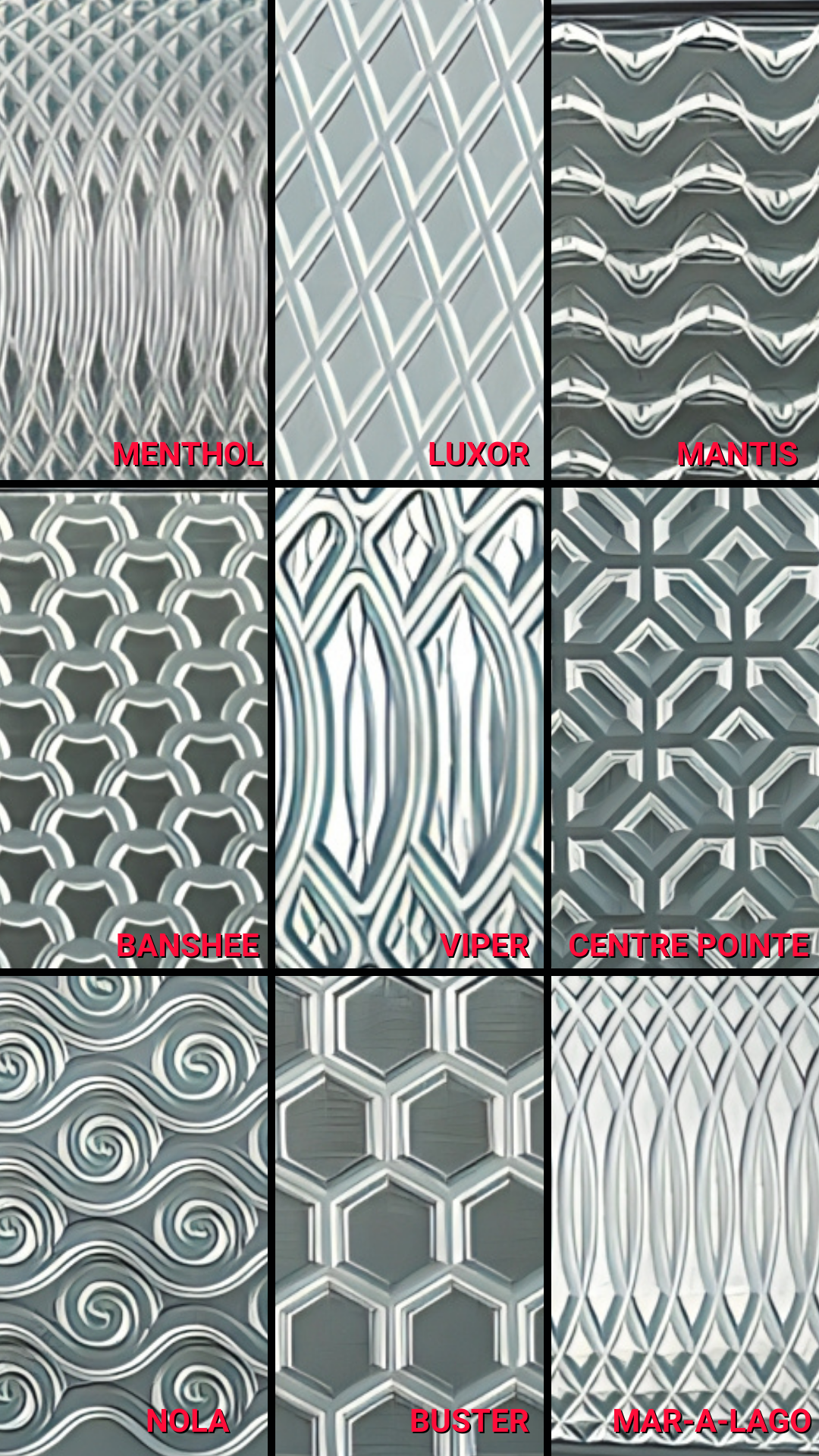
"proprietary" is our middle name
DESIGN
We’ve applied the same quiet professionalism from our Defense and Aerospace background to our approaches in the golf world. Each model we offer is designed from the ground up to fit a specific play style, and undergoes a manufacturing feasibility study, with emphasis on desired balance, weight, and ground contact. We constantly aim to improve and challenge the status quo of the short-game, and each of our initial Front Nine models demonstrates their own uniqueness.
Within "The Front 9" you'll find proprietary face engraving and geometries, each with a unique look and consistent feel, while also offering the familiar “face-milling” process that all golfers are familiar with.
AXP will never show you a “render” or simulated putter; all photos are the real final products without modification.
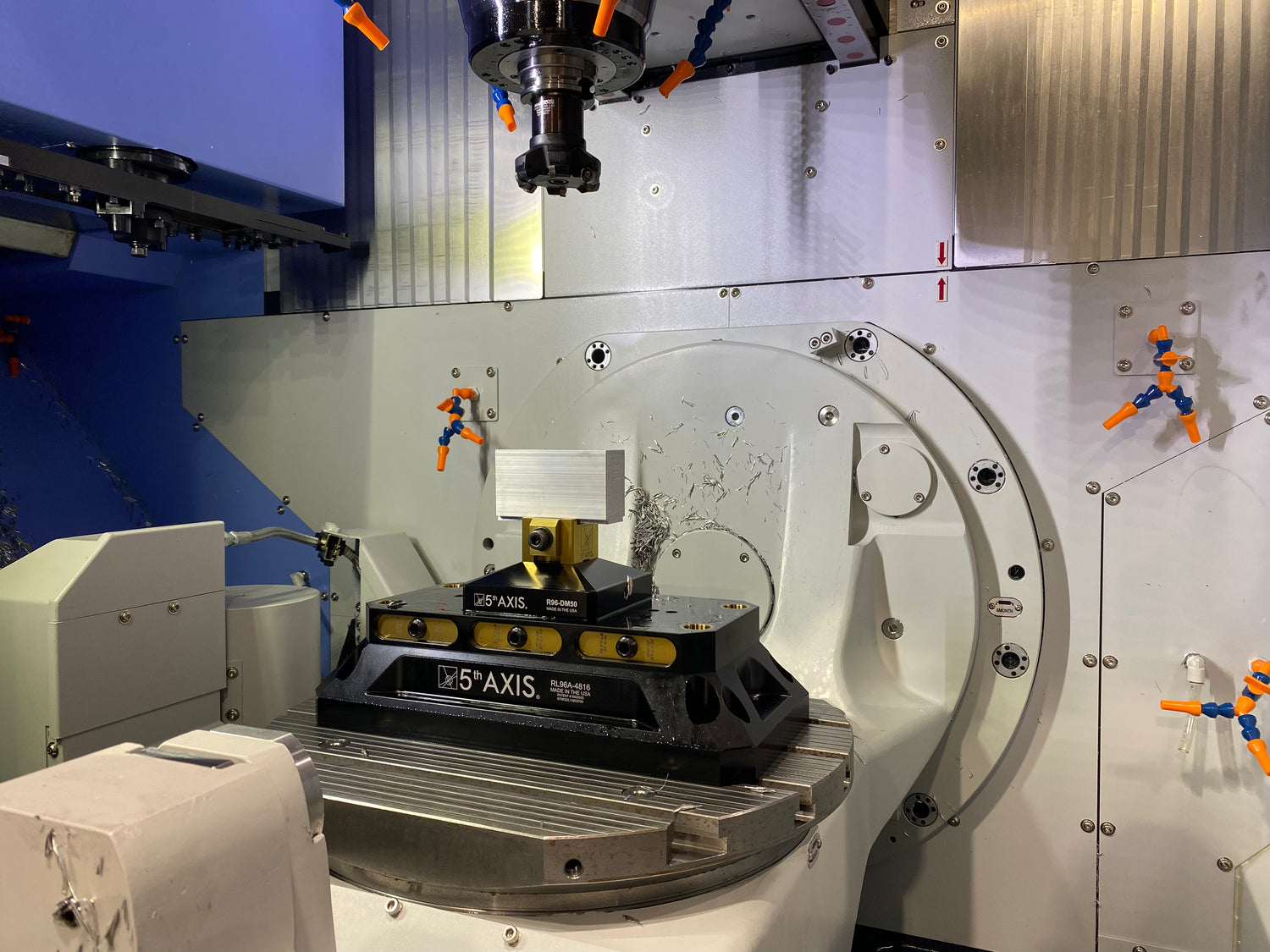
MODERN APPROACH, TRADITIONAL VALUES
OUR FACILITY
Here at AXP HQ, in The Woodlands, Texas, we operate multiple forms of CNC controlled machines, with specific emphasis on simultaneous 5th axis mills. These are the same machines that create the gas generating turbines for jet engines, implants for advanced medical procedures, and equally complicated and confidential defense and aerospace components. Our machines give us the ability to create the detailed geometry that our models embody, without the limitations of out-dated milling processes that most of our competitors use.
Your AXP putter is crafted from a solid block of GSS, utilizing the cutting edge of aerospace and defense machining, on machines comparable in cost and performance to a new Ferrari.
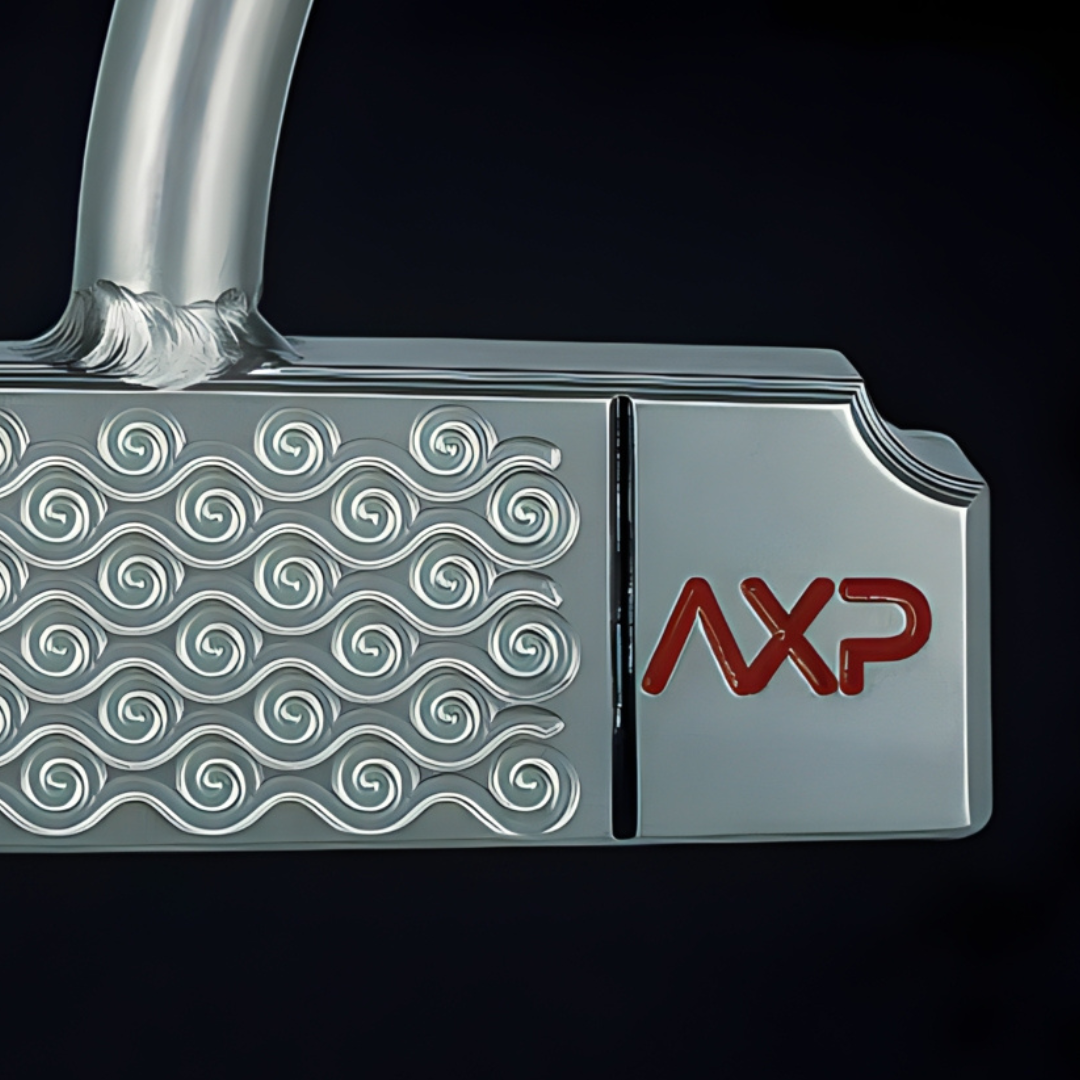
A PROFESSIONAL TOUCH
HAND-WELDED
While we utilize some of the most advanced machining approaches available, you can rest assured that each putter is handcrafted. This is demonstrated, in part, by our hand-welded hosels. While 303 Stainless Steel is very challenging to weld, our team accomplishes smooth and strong bonds. Each AXP putter has been hand-fitted, and welded by our professional TIG welding team right in the heart of Texas.
There’s no mistaking the appeal and appearance of a well laid bead on your putter.
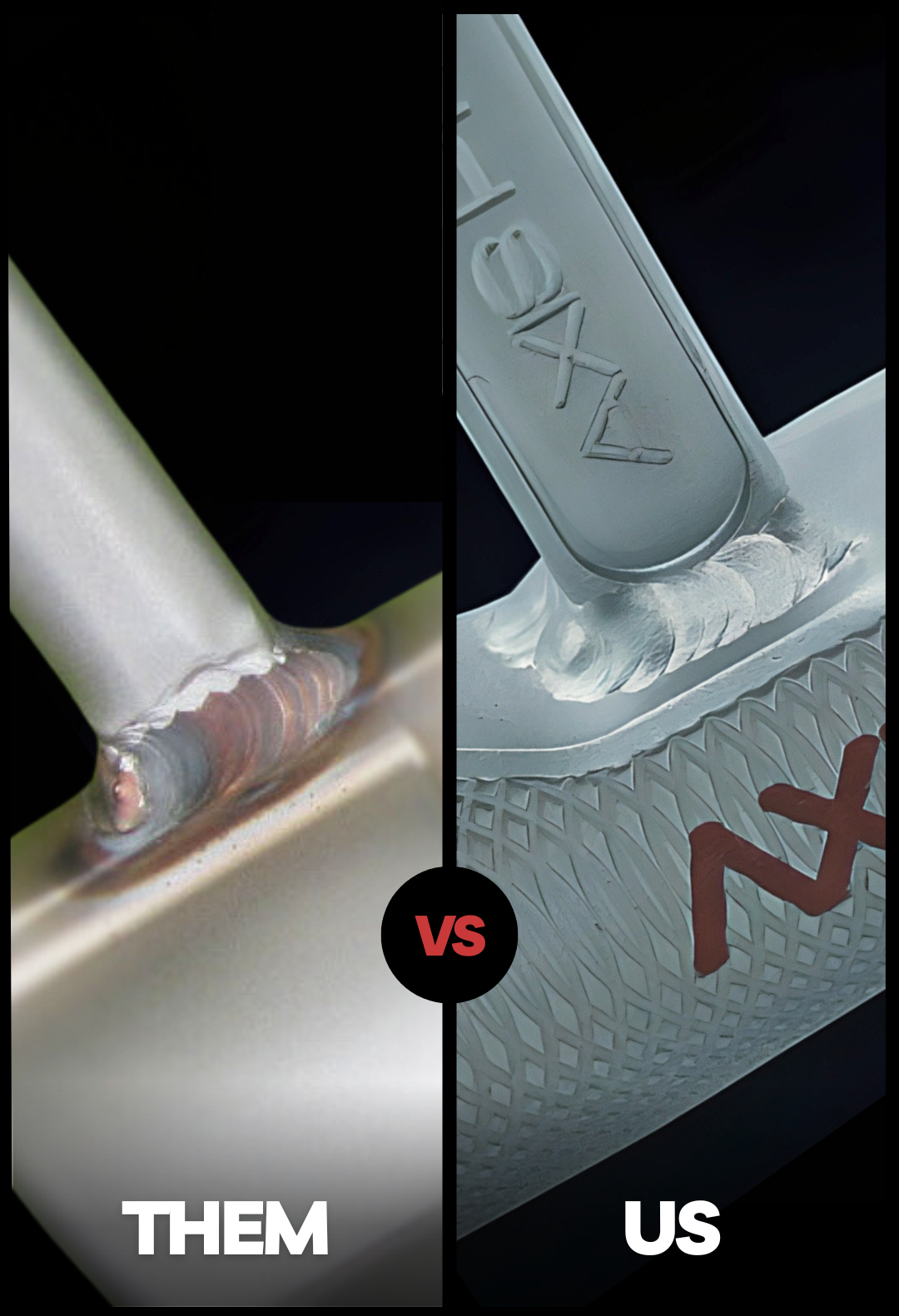
RESTORATION
PASSIVATION
After your putter is TIG welded, it undergoes a detailed cleaning process, and is chemically passivated. Specific to chromium containing alloys, the process of welding can damage the oxide/chromium layer which can weaken the otherwise naturally corrosion and rust resistant stainless steel.
Passivation both enhances the visual appearance of the welds, and restores the corrosion resistance of your putter. AXP uses an environmentally friendly process, requiring no special handling or risk to our staff or you.
Don’t be fooled by competitors who slap paint or simply media blast a welded area - this is not a restoration of the strength and corrosion resistance that passivation provides.
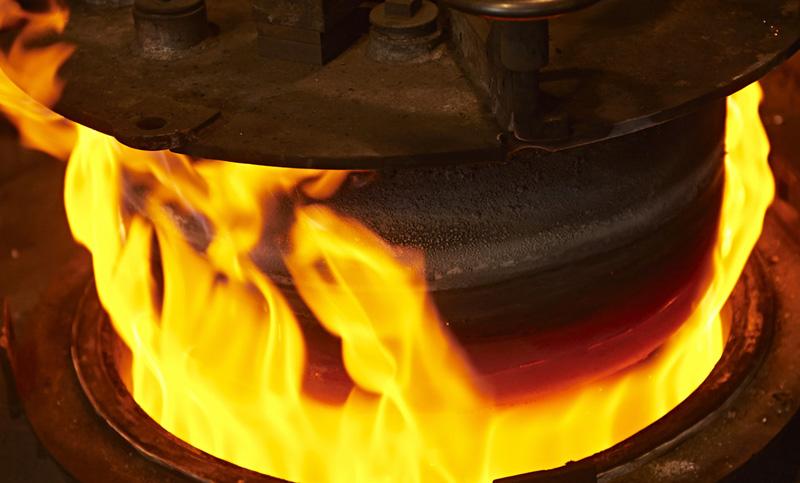
POST-PROCESSES
STRESS RELIEVING AND ANNEALING
If you’ve made it this far, you’ve garnered that we take post-processing of our models very seriously, and we have a few more steps before your AXP putter is complete. After passivation, each putter is put through a combination of stress relieving (not shiatsu massage) and annealing. Stress relieving is an important procedural step, utilizing a kiln capable of up to 2,000 degree Fahrenheit temperatures, the process smoothes out the internal grain structure of the metal itself. Any structural changes incurred from the time the bar stock left Germany, to machining and welding here in Texas, are completely restored.
We take the time to do a two-stage annealing process in conjunction with the stress relieving procedure, further softening and strengthening the material, to create the best possible putter we can deliver.
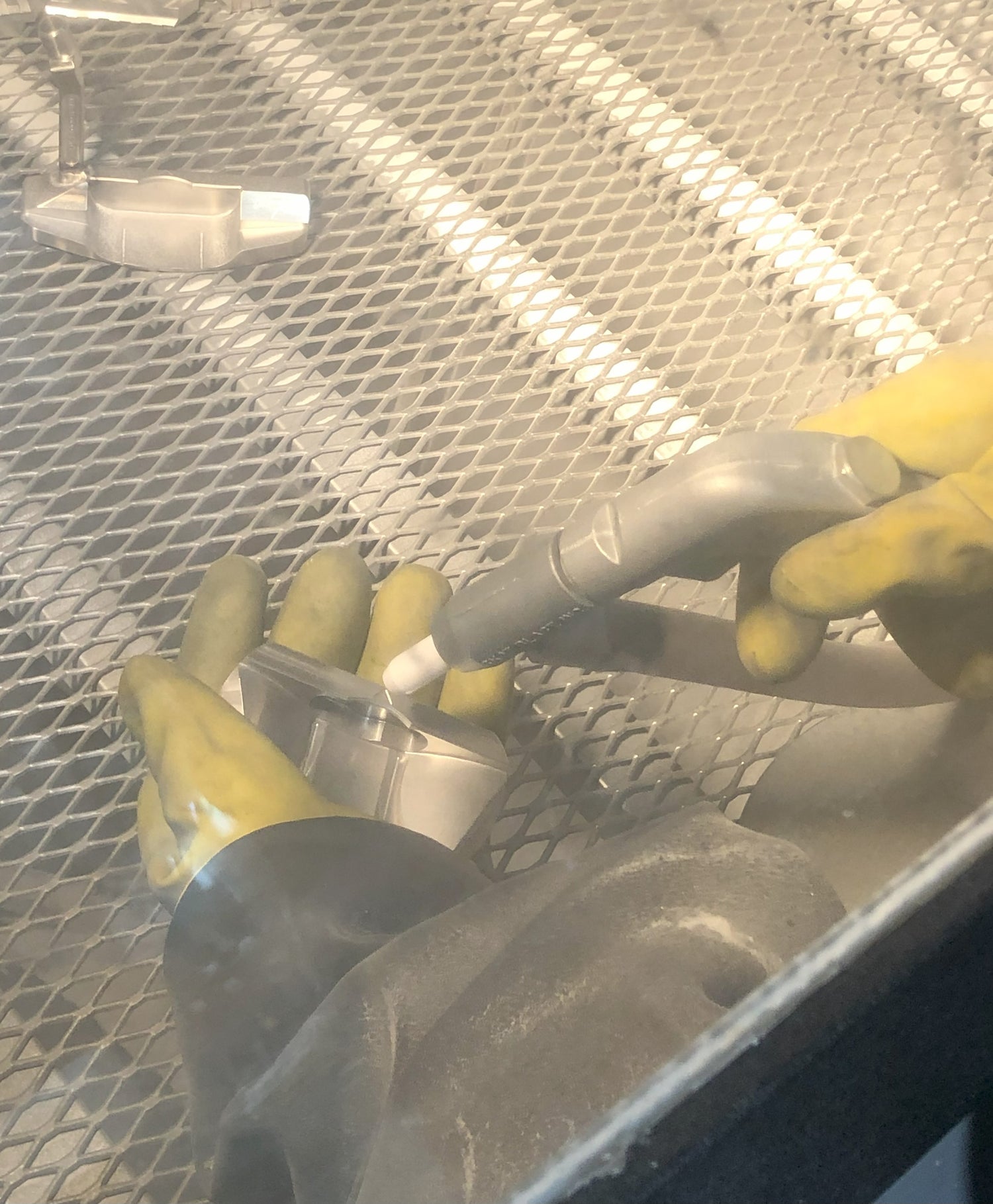
SMOOTH, SAFE FINISHES
GLASS BEAD BLASTING
Finally, your putter is blasted and our post-processing is finished. Our glass bead blasting ensures the uniform, appealing, and smooth satin finish in our standard colorways. The blasting media contains no free-silica and presents no health hazards to our staff or the environment and used glass blasting media is recycled.
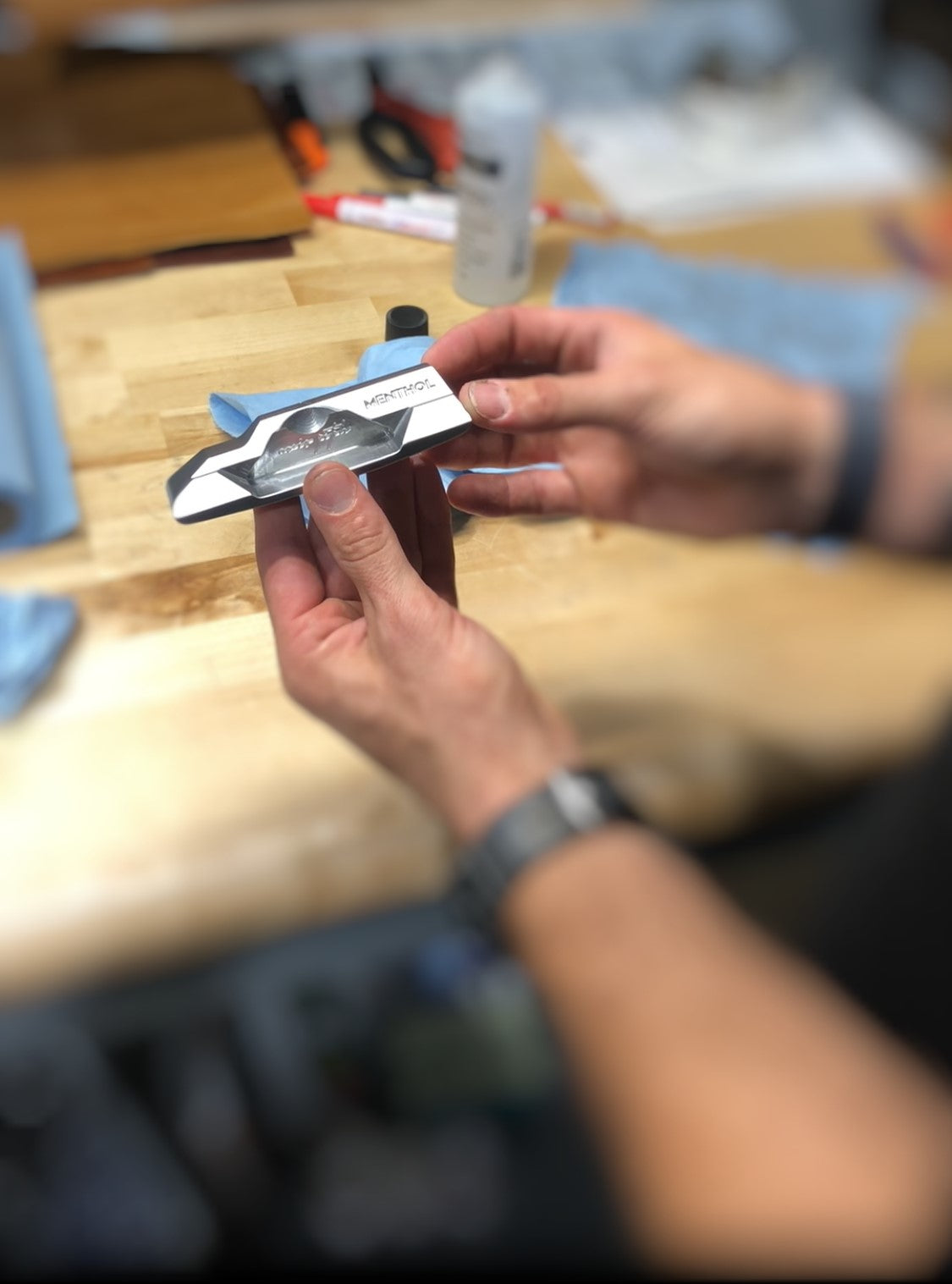
FROM OUR HANDS TO YOURS
FINAL INSPECTION
Each finished putter is inspected to ensure dimensional accuracy, weight, and appearance by our inspectors. In keeping with traditional manufacturing, each model carries an ‘arsenal mark’; a hand-stamped marking showing both the location of manufacture and the inspector(s)’ initials struck into your putter.
We hope that you enjoyed learning about the processes we employ at AXP to bring you the best products in the industry.